It would not be a surprise if you, or someone close to you, has an old chair tucked away in the depths of the basement or up in the attic. It’s there because you like it too much to get rid of it – it holds fond memories, it was your Great Aunt’s, the carving on the back is intricate and appealing – but there’s one problem; your cherished chair has a caned seat and for years there has been a gaping hole in it. Not much use in a chair with a missing seat, but who the devil knows how to cane anymore? More people than you think.
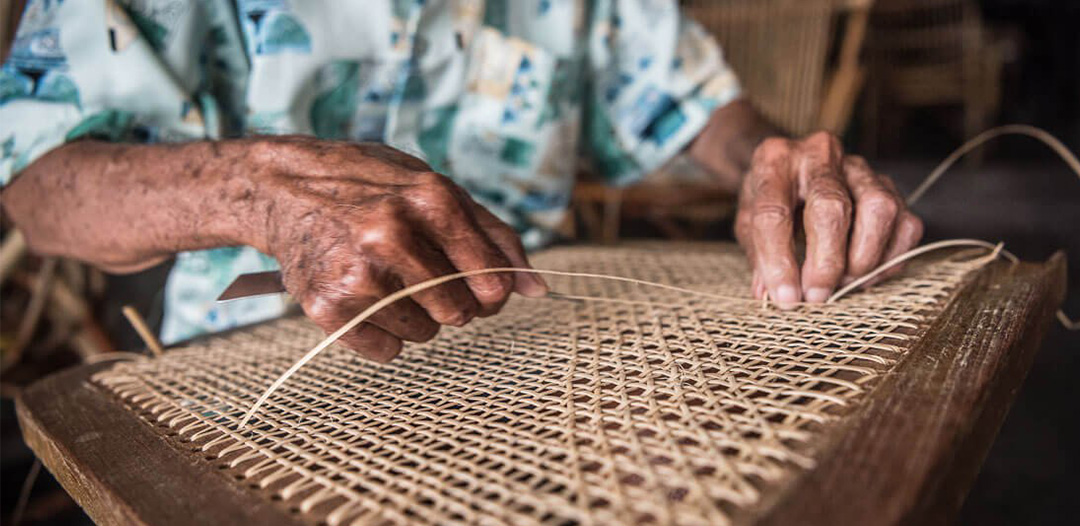
If you type “caning” into your favorite search engine you will probably first hit corporal punishment, Singapore, and Michael Fay, but have faith and keep scrolling until you find caned furnishings. It turns out that caning, a strong, natural, woven matting used primarily for seating, has been around for a very long time. Nowadays, it is a fairly scarce craft, but not a forgotten one.
The most oft-noted example of ancient caning is the camping daybed of King Tutankhamen (1325B.C.), a folding bed frame with caning across each section that served as the sleeping surface, once unfolded. The lightness of the cane made this early cot quite practical for carrying off on the boy king’s frequent hunting excursions. That it survived in his famous tombs is also a testament to the longevity of the material.
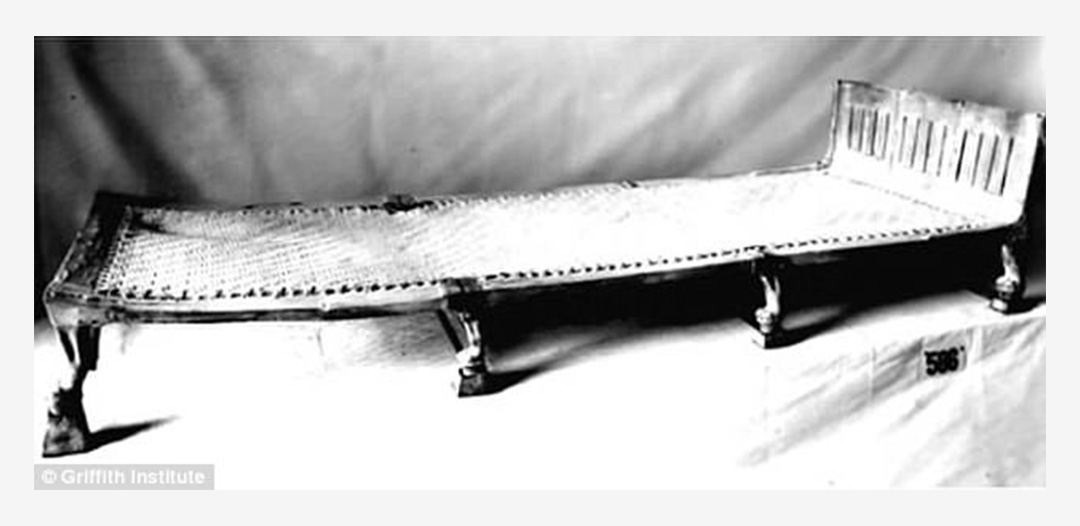
Cane comes from the rattan vine (Calamus), a climbing species of palm that grows wild throughout Southeast Asia. The palm grows vertically, utilizing thorn-like hooks to grab onto any neighboring structure, making it the ultimate “social climber”. As it grows, the trunk stays uniform in diameter, ranging from one to two inches thick. The strands used in caning are derived from the bark of the rattan palm.
Extremely lightweight and non-porous, it doesn’t warp or crack and is not prone to mold or insect infestation. The vine’s inner portion is used for making rattan and wicker, as well as for basketry; hence, caning, wicker, and rattan often get jumbled together, although they are each distinct crafts.
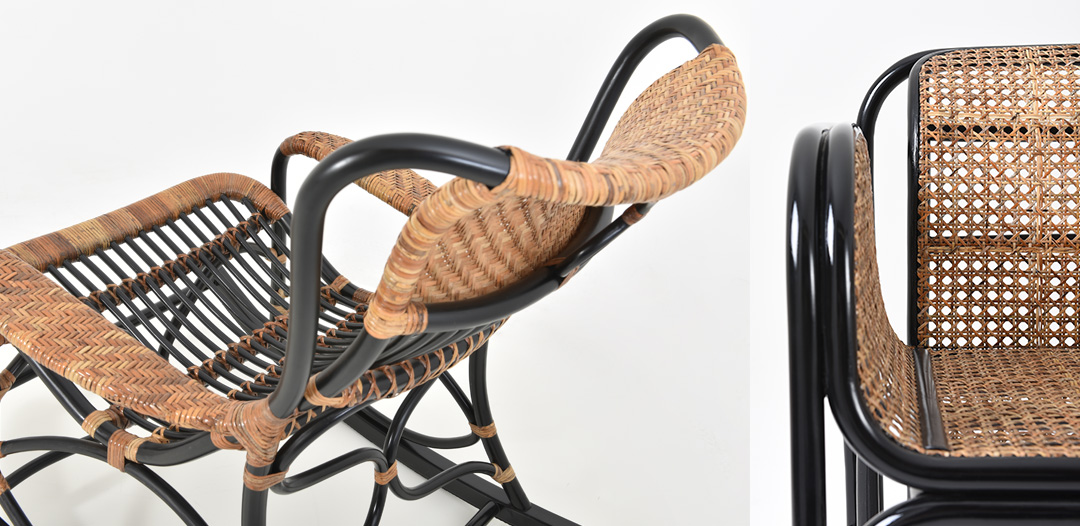
The natural characteristics of caning strips mentioned above led to the explosive growth of the product in the 1600s. European colonists drawn to Asia by the tea and spice trade, found the material to be indispensable in the making of furniture for the tropical climes of the colonies. It was also an easily exported product due to its lightness and durability. That popularity continues today.
There are three main patterns in caning methods:
-The first and simplest is the “hole to hole”. This involves a frame with holes placed equidistantly around its perimeter. The cane strips are then woven in a vertical and horizontal crisscross forming a plain checkerboard pattern.
– The second, known as wide brim caning, has a tight, solid weave and resembles more of a rattan look.
-The third style is cane webbing. Its most prominent pattern, 7 Step Caning, results in the traditional hexagonal hole design we find most familiar. This involves weaving the strips horizontally, vertically as well as diagonally.
One of a few iconic caned pieces, perhaps the most famous and most copied, is the Thonet No 14 Chair designed by Michael Thonet and brought to market in 1859. What has come to be known as the “bistro chair”, it is the classic bentwood-shaped back with a woven caned seat, in the familiar 7 Step pattern. The original comprised of only six wooden pieces and a handful of screws and bolts.
The chair could easily be shipped disassembled and put back together at its destination, requiring no particular skills or craftsmanship. Distributed by the Thonet Chair Company, it became one of the earliest examples of mass-produced furniture.
The contemporary cousin of the bistro chair is the Cesca Chair designed by Marcel Breuer in 1928. It is believed to be the first chair frame made with tubular steel, and it too sports a 7 Step pattern caned seat and back.
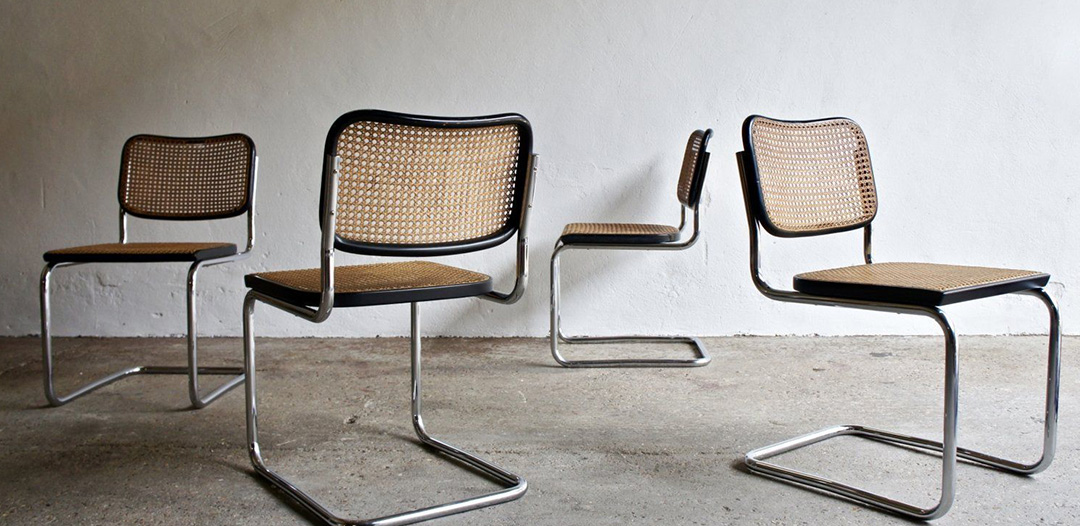
It is the diametric opposite of its cousin, with a very angular shape, sharp but smooth corners, and an appearance of floating rather than standing on four legs. It was also mass-produced and is still widely available from a variety of companies. Original Breuer chairs have a strong secondary market value as well.
But what about Grannie’s broken chair in the attic?
Rest at ease; it is salvageable. That same internet search we spoke of before led to many restoration sites that undertake cane replacement, as well as rattan. Further digging also led to companies offering pre-woven sheets of 7 step caning, along with spline – the material used to hold the caning in place – and best yet, instructions! If you’re feeling a little nostalgic and a wee bit crafty, a little DIY ingenuity can bring your treasure back to its rightful spot in the living areas of your home.